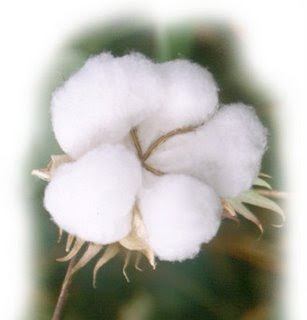
Sabemos que desde antes de la revolución industrial el algodón es la fibra de mayorconsumo en el mundo y por lo tanto los procesos textiles usados para la manufactura delmismo son conocidos universalmente. Además cada día se usa más la mezcla de algodóncon poliéster, que es la fibra que cada día cobra más importancia y en un futuro cercanoserá la fibra de mayor consumo mundial, de hecho ya lo es para muchas aplicaciones yusos.Considerando que la mitad del poliéster producido en el mundo se usa como fibra corta,podríamos deducir fácilmente que el proceso de hilatura de fibra corta representa más del80% de la producción mundial de hilos hilados. De aquí la importancia de conocer esteproceso y sus diferentes variables.
.b) Siembra con acolchado de plástico
.Siembra sobre l
Siembra con acolchado de plástico
Es una técnica muy extendida y consiste en colocar unos plásticos en la superficie del terreno mediante una maquinaria muy completa. Esta maquinaria consiste en una sembradora neumática la cual aplica los insecticidas de suelo, los abonos y la colocación de una lámina de plástico.La técnica del acolchado consiste en que la línea de siembra quede centrada en la lámina de plástico. Se deben de realizar una serie de perforaciones en el plástico para que la planta salga por ahí. La película de plástico sirve como cámara protectora de la planta.Si existe condensación de vapor las temperaturas no son muy elevadas, no se debería perforar los plásticos. Para evitar las altas temperaturas si se debe perforar el plástico pues las altas temperaturas producirán quemaduras en las plan
Ventajas de siembra con plásticoAsegura la nesciencia de la semilla por lo tanto asegura un buen ahorro de semilla. El terreno al estar protegido con acolchado mantiene durante más tiempo la humedad del mismo sin formación de costra por consiguiente más facilidad para la nesciencia de la semilla.2. Mantienen unas temperaturas mínimas de 4 a 5ºC por encima a la temperatura que produce el medio exterior. Mantiene gran parte de horas del día a unas temperaturas inferior a los 15ºC permitiendo así un desarrollo de la planta no interrumpido
Inconvenientes del uso del plástico
Supone un gasto de ahorro en el cultivo, pues además de tratarse el algodón de un cultivo caro la implantación del acolchado le supone aún más gastos.2. Las lluvias en primavera producen una especie de bolsas en el plástico que empujan hacia la planta e impiden el desarrollo de ésta. En este caso abría que perforar el plástico para no dar problemas.3. Los patógenos de suelo pueden manifestarse con una mayor agresividad bajo plástico pues favorece más su desarrollo
Siembra en lomos:
La sembra en lomos permite un oreo del terreno y una mayor acumulación de temperaturas en el terreno sin pérdidas de excesivas de la humedad. Con terrenos llanos y unas lluvias frecuentes se originarían encharcamientos en los suelos de cultivo que acabarían con la plantación, en cambio, terrenos alomados el agua circularía por el valle del lomo y la planta no moriría por asfixia.Las últimas tendencias son efectuar una siembra temprana para igualmente, realizar una recolección temprana con un mayor rendero
El marco de plantación que se realiza es de 0.95 m entre hileras para recolección mecánica. Para cultivos en secano se recomienda una anchura de siembra de 0.75 a 0.80 m de distancia entre hileras ya que la recolección se realiza a mano.
Cuando las plantas de algodón alcanzan un tamaño de 5 a 10 cm de altura se procede al aclareo. En él se pretende eliminar un número concreto de plantas que interfieren unas con otras dejando de este modo unas 10 plantas por metro lineal, es decir, una plantación de 100.000 plantas/ha. Es una operación que se realiza a mano por lo tanto supone un costo en mano de obra.
Al comienzo de la formación de la cápsula se debe detener el desarrollo vegetativo de la planta. Para ello se realiza el despunte que consiste en cortar a mano los extremos o brotes herbáceos de las ramas más altas.En caso de no realizar el despunte de forma manual se pueden utilizar productos químicos que originen disminución en el crecimiento de la planta como es el caso de Cloruro de 1, 1-dimetil piperidinium
Recoleccion mecanica
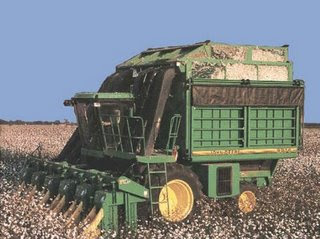
Un algodón mucho más limpio y mejor seleccionado. Se utiliza cuando se trata de
Pequeños cultivos en países poco industrializados como en el caso de Colombia.3. Desmotado
Este proceso se hace en instalaciones que están cercanas a las zonas de cultivo.
Generalmente son empresas particulares que prestan el servicio a los cultivadores.
En el desmotado se llevan a cabo las siguientes funociones
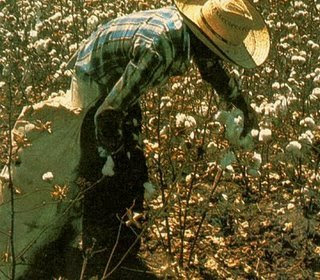
3. Desmotado
Este proceso se hace en stalaciones que están cercanas a las zonas de cultivo.
Generalmente son empresas particulares que prestan el servicio a los cultivadores.
En el desmotado se llevan a cabo las siguientes funciones:
Secado inicial del algodón
Limpieza severa del material
Separación de la fibra y la semilla (desmotado en sí)
Formación de una paca de unos 250 kg.
Toma de la muestra para la asignación del grado.
Una vez formadas las pacas se dejan expuestas a la intemperie por un período de 24 horas (cuarentena), con el fin de prevenir incendios debidos a las fuertes presiones internas que se acumulan durante el embalaje y a la alta inflamabilidad de esta final
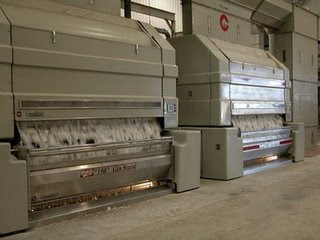
Clasificación de el . algodón es llevado a las bodegas de la empresa donde se almacena y se extraen muestrasde cada una de las pacas con el fin de hacerles los análisis respectivos después de una ambientación previa de unas 24 horas en el laboratorio de fibras, el cual tiene un ambiente
controlado a 21°C y 65 % de humedad relativa.
Los análisis más comunes que se le hacen a las fibras de algodón son los siguientes:
a) LongitudSe hace en el Fibrógrafo y se determinan los siguientes valores
Longitud al 50 %: Indica la longitud mínima que tienen el 50 % de las fibras de las
muestras
Relación de uniformidad: Es la relación entre la longitud al 50 % y la longitud efectiva,
expresada como porcentaje. Este valor oscila entre 45 y 48 %.
La longitud efectiva es la base para realizar algunos de los ajustes en las máquinas dehilanderíab)
finura de las fibras se puede medir en micras, dtex, mtex o denier pero en el caso del
algodón la finura se mide en unidades IMF (Indice Micronaire de finura). Este es un
método que mide la caída de presión de una corriente de aire que se hace pasar a través d
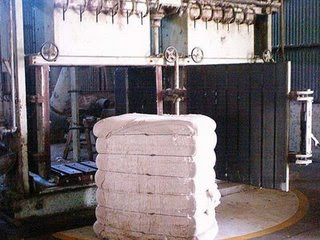
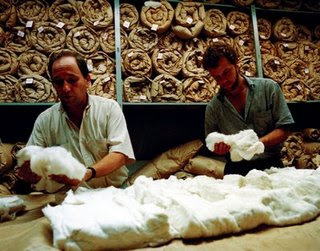
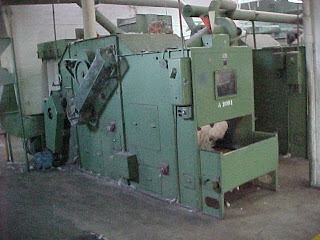
Partes de la Maquina
Blendomat: Esta compuesto por dos cilindros disgregadores que depreden los copos de algodón de las pacas, y tres cilindros de apoyo. Sirve para abrir y mezclar el algodón de acuerdo a los planos de distribución sin levantar polvo.
Abridora de pacas
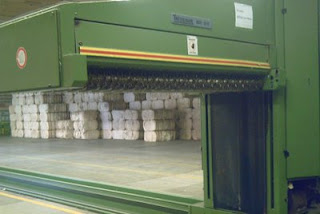
Le proporciona succión al Blendomat, encaminando las partes del algodón hasta el bypass
Condensador:
Recolectar cinta:Tome un carro de la bodega de desperdicios y recoja la cinta que encuentre en los tarros destinados para velo y cinta en la zona de cardas.
Pescar pacas:
Material Saliente.
3. Variedad o semilla.
4. Lote (identificación del agricultor)
Divisa:
Protección Auditiva
Debido al alto ruido producido por las diferentes máquinas existentes en el salón de preparación hilados (cardas, estiradoras, mecheras, hiladoras). Es indispensable usarlos ya que pueden ocasionar daños irreversibles en el oído.
Respiradores Deshechables
Estos son utilizados como prevención, ya que el ambiente del salón tiene muchas partículas que pueden llegar fácilmente a los pulmones produciendo muchas enfermedades.
con el constante trajín del operario el cuchillo debe de llevarse en su respectivo estuche para evitar así un accidente.
Normas Especificas Del Oficio.
Utilizar los implementos de seguridad que requiere el oficio.- Al hacer los arrumes de alambrón y zunchos, hágalos de tal manera que pueda transportarlos fácilmente al sitio de almacenamiento- Cuando efectúe la limpieza y colocación de la paca en el punto de apertura, verifique la alineación, con el fin de no bloquear el Blendomat.
No guarde escobillones, escobas u otros objetos dentro de las cavidades internas o externas de las máquinas.- Mantenga siempre en orden el lugar de trabajo.- En caso de incendio, apague la maquinaria y avise inmediatamente a los bomberos .- No desempeñe oficios que no se le han autorizado o que no tenga conocimiento de ellos.
1. Todo accidente por leve que sea debe ser informado inmediatamente al Supervisor.
2. No retire las guardas de seguridad con la máquina en movimiento.
3. No opere maquinaria o equipo que no conozca
4. El mecánico es quien debe reparar su máquina.
5. Al subir o bajar escaleras, hágalo siempre de frente a ellas, nunca dándoles la espalda
.6. Mantenga aseado y ordenado su puesto de trabajo
7. Evite el uso de mangas largas, ropa ancha, camisas por fuera, joyas y pelo largo suelto
8. Use los equipos de protección personal indicados para su oficio
9. Si su trabajo requiere de cuchillos, ganchos o tijeras, llévelas siempre en su respectivo estuche.
10. No tape los equipos contra incendios tales como: Hidrantes, gabinetes, extintores y salidas de emergencia.
11. Lleve siempre consigo los documentos de identificación (cédula, tarjeta del ISS).
12. No haga reparaciones eléctricas, informe inmediatamente al supervisor o al departamento eléctrico.
13. Utilice únicamente herramientas en buen estado.
14. Informe al supervisor o un miembro del comité de seguridad los riesgos que observe en su lugar de trabajo, en las máquinas o equipos.
15. Evite los juegos y charlas en su puesto de trabajo.
16. Seque los regueros de aceite y los charcos de agua en el piso.
17. En caso de incendio avise inmediatamente a la brigada.18. Evite el uso de relojes, anillos, pulseras, cadenas.
Abridora moderna.
La abridora de balas programable BLENDOMAT BDT 019 combinada con el mando de microcomputadora BLENCOMMANDER'BC satisface todas las las condiciones que se exigen en la practica de una abridora de balas automática y ofrece una serie de ventajas especiale
1. granada taptabilidad
2. gran numero de balas de alimentación
3. Numerosas posibilidades de mezcla
4. apertura fina con preservación de la fibra
5. Alta producción
6. versatilidad de producción
7. facilidad de servicio
8. seguridad de funcionamiento
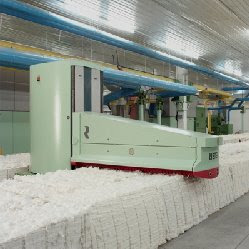
el flujo de abridora
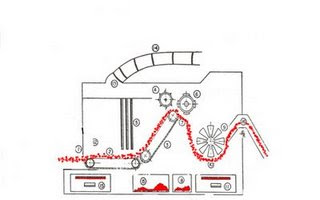
PROCESO DE BATANADO Y ENROLLADO
Las fibras provenientes de los equipos de apertura y limpieza intermitentes son colocados en la tolva alimentadora numero 1, en donde por acción de la estera horizontal y estera vertical la Fibra es llevada hasta la parte superior donde la regula, la carga por el giro de un desprendedor Oriente hacia la esfera horizontal numero 2 y de allí por medio de su giro la fibra es alimentada por dos cilindros que la presentan a la acción del primer batidor de regla debido a su gran velocidad este golpea las fibras y las lanza contra las rejillas para que a través de ellas se efectué una limpieza muy importante (partículas mas pesadas). Las fibras disgregadas son lanzadas a un par de des condensadores las cuales debido a su gran velocidad forman una manta de fibras, la que es evacuada por un par de rollos extractores. La masa de fibras es desplazada sobre la mesa de conducción y al final de ella unas esteras verticales llevan la fibra a la parte superior para que el Doffer desprendedor los golpee y las lance al interior de la tolva o cámara, donde se mantendrá un volumen constante de carga. Unos cilindros extractores vacían la manta de fibras y la orientan al sistema de orientación el igualador o mecanismo de alimentación, en donde a través de un pedal y un cilindro de fibras son pinzadas y presentados controladamente a la acción del segundo batidor de púas, el cual a través de púas penetra en la masa de fibras peinándolas y lanzándolas contra las respectivas rejillas, otro par de condensadores decepcionan las fibras sueltas formando una napa que es evacuada por los cilindros y orientada a la sección calandra dora, donde 4 cilindros metálicos que soportan entre si una alta presión le imprimen compatibilidad a la napa definiendo su estructura y orientándola a la acción de un par de enrolladores para que sea envuelta en un núcleo metálico hasta conseguir un rollo de longitud determan
flujo del bantan
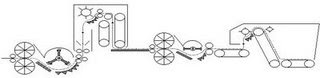
MAQUINAS: CARDA
PROCESO
El rollo de napa es colocado sobre el cilindro desenrollado, y este es desenvuelto por el giro del cilindro que va desplazando la napa a través de la mesa de alimentación para que al final de ésta y en conjunción del cilindro alimentador, pinzan las fibras y las presentan a muy baja velocidad a la acción del Lickerin, el cual a través de sus púas y debido a la gran velocidad penetra en la masa de fibras disgregándolas y danzándolas hacia la parte delantera. Las impurezas mas pesadas son extraídas por cuchillas aprovechando la acción de la gravedad y de esta manera se hacen la ocasión de la limpieza. Las fibras siguen en suspensión de la superficie del Lickerin y en el punto de tangencia de este con el gran cilindro son arrebatadas debido a su mayor velocidad superficial.
El gran cilindro transporta las fibras hacia la parte superior para que conjuntamente con los chapones se efecto el cardado propiamente, consistente en desenredar las fibras, separando las mas cortas y algunas impurezas que quedaran atrapadas por los chapones y extraídas como El gran cilindro le entrega las fibras al Doffer en su punto de tangencia debido a la muy baja del Doffer, va decepcionando las fibras y condensando hasta formar un velo, el cual es evacuado por el giro del Doffer en la parte inferior yen le punto de encuentro con el cilindro desprendedor el velo cambia de trayectoria y es orientado hacia el interior de la trompetilla o embudo para formar la cinta, a la cual se le imprime compatibilidad por dos cilindros calandradores, que la llevan hacia adelante y la orientan hacia la parte superior del coiler, en donde hay un par de calandrines y otra trompetilla que complementan la acción del calandrado y de esta manera definir la estructura de la cinta para que finalmente sea colocada o devanada en forma de es un desperdicio
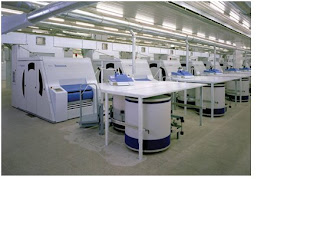

En el manuar se cumplen las siguientes funciones:
Doblaje: Por cada lado de trabajo se alimentan 6 u 8 cintas provenientes de cardas con
el fin de homogenizar el material.
Mezclado: Las cintas alimentadas pueden ser de diferentes fibras, por ejemplo, 4 cintas
de algodón y 4 cintas de poliéster.
Estirado del material.
Se produce una cinta con peso por unidad de longitud establecida.
Se devana la cinta recién formada en un bote de tamaño específico.
Definición de estiraje
El estirado no provoca el alargamiento de las fibras, sino que consiste en una reducción de
la masa de fibras mediante desplazamiento longitudinal de unas fibras con respecto a otras.
Mediante el mismo las fibras se paralelizan y orientan en el sentido del eje de la cinta.
El estiraje no se práctica sobre una cinta unitaria, sino sobre un conjunto de cintas por
doblaje.
El tren de estiraje de un manuar esta conformado por varios juegos de cilindros, los cuales
tienen velocidades periféricas cada vez mayores hacia adelante. El estiraje se produce pues
por la diferencia entre la velocidad de salida con respecto a la velocidad de alimentación.
El valor del estiraje se expresa con un número a dimensional Por ejemplo, un estiraje de 5
en una máquina, quiere decir:
Que en la máquina, la velocidad de entrega del material es 5 veces mayor que la
velocidad de alimentación del mismo.
Que el peso por unidad de longitud del material entregado es 5 veces menor al peso por
unidad de longitud total alimentado a la máquina.
Que por cada metro de material alimentado a la máquina se producen 5 metros a la
salida de la misma.
Casi todas las máquinas de la hilandería tienen estiraje.
Definición de doblaje
En los diferentes procesos, denominados doblaje al hecho de alimentar a la entrada de la
máquina, un cierto número de cintas que provienen del proceso anterior y que serán
estiradas en conjunto y re ensambladas en una sola cinta a la salida de la máquina. Por
ejemplo, decimos que el doblaje es 6, cuando se reúnen 6 cintas a la entrada de la máquina
para obtener solo una a la salida.
El doblaje tiene por objeto mejorar la distribución de las fibras y de asegurar la
homogeneidad de estas, sobre todo en el caso particular de las mezclas de diferentes tipos
de fibras. Es evidente que cuanto más elevado sea el número de doblajes, mayor será la
reducción de la irregularidad en la cinta producida.
Con el fin de conservar en la cinta su peso original, el doblado debe ser compensado por el
estiraje. Si es necesario un afinamiento progresivo de la cinta (preparación de la hilatura),
el estiraje debe ser mayor que el doblaje.
El número total de doblajes en todo el proceso de hilatura es igual al producto (y no a la
suma) de los doblajes en cada proceso. Es el doblaje total quien determina, por así decirlo,
el grado de regularización. Con las máquinas antiguas esta cifra era elevada, pero
actualmente es considerablemente reducido gracias a que las nuevas máquinas disponen de
mejor control de las fibras y de sistemas de autorregulación.
Normalmente se dan varios pases de manuar con el fin de conseguir mayores niveles de
mezclado, homogeneización y orientación de las fibras. Para hacer referencia a este
proceso se habla entonces de manuar primer pase, manuar segundo pase, manuar tercer
pase, etc.
Los Manuares pueden tener 1 o 2 puestos de trabajo, o sea que entregan hasta dos
cintas a la ve
concepto de ecartamiento en los manuares
Es el ajuste principal en las máquinas de hilanderías, especialmente en el manuar. Se define
como la distancia comprendida entre dos puntos de pinzaje consecutivos. Para determinar
el Ecartamiento óptimo es necesario tener en cuenta la longitud efectiva de las fibras
Material Entrante
Material SalienteEl material saliente de la estiradora es una cinta de fibras paralelizadas, mas limpias y de un peso de 70 granos por yarda, este material es depositado en botes plásticos de 20 pulgadas de diámetro por 42 pulgadas de altura y tiene una capacidad de 4200 metros de cinta.Ver foto.Los botes tienen un resorte interno para obtener un enrollado y desenrollado optimo de la cinta, el peso del bote vació es de 12.5 Kg. y el peso de la cinta es de 20.8kg por bote, la estiradora produce un estiraje del 7%.La envoltura de la cinta debe de cumplir los siguientes requisitos:- Envoltura uniforme.- La cinta debe de estar limpia. Libre de polvo, basura, grasa, etc.- No se debe de revolver material de diferentes mezclas.- No debe presentar tramos gruesos ni delgados.
Divisas.
NORMAS DE SEGURIDAD
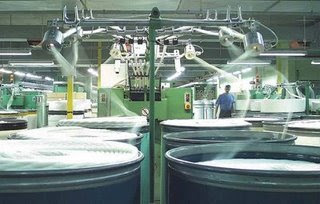
flujos de manuar o estirada
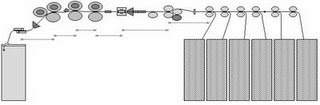
Su objetivo es reunir varias cintas en una sola. Están destinadas a la fabricación de un rollo de cintas de longitud determinada; la alimentación es de 16 a 20 cintas. Éstas son entregadas a una mesa formando una capa de material, luego pasan a un par de cilindros calandradores y posteriormente a los tambores formadores del rollo. La cinta recibe una tensión.La reunidora súper-lap no necesita el paso del manuar, es alimentada con el velo de cardas; posee un pequeño manuar y forma un rollo de cintas superpuestas.
flujo de reunidora
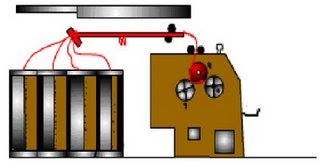
En la peinadora se cumplen las siguientes funciones
Alimentación de 4 o 6 rollos de cinta por cada la
El subproducto obtenido en la peinadora se llama NOIL, equivale aproximadamente al 15%del material alimentado y es aprovechado para hacer hilos bastos.El proceso de peinado resulta demasiado costoso y solo se práctica cuando se desea obtenerhilos muy finos y / o de muy alta calidad.Después de este proceso siempre se hacen 1, 2 ó 3 pases de manuar con el fin de compensaren las cintas irregularidades introducidas en el desprendimiento y posterior empalme de lasfibras, durante la difícil operación de peinado. También tiene como fin mezclar el algodónpeinado con otras fibras como el poliéster.
NOTAEl peinado solo se práctica a rollos de cinta de algodón 100 %, nunca con mezclas.Estas se pueden hacer una vez el algodón ha sido peinado.
INFLUENCIA DEL PEINADO EN EL PROCESO Y EN EL HILO
Con algodón peinado se pueden producir hilos más delgados por la uniformidad de lalongitud de fibra
Facilita la hilatura al eliminar las grandes variaciones en la longitud de las fibras
Por su mayor grado de paralelización y ordenamiento de las fibras produce hilmenospelu
Se pueden producir hilos más resistentes, ya que las fibras largas tienen una mejorcohesión entre sí por tener una área mayor de contacto.
Se producen hilos más lustrosos y limpios.
Funciones de Operario.Cambiar taco vacío por rollo de napa: Cuando la señal de paro y la pantalla estén señalandcambio de napas de trabajo, ubíquese al frente de la máquina y gire la perilla de color negro hacia la derecha para desasegurar la tapa protectora.Levante completamente la tapa hacia arriba.
Material Saliente
El material saliente de la peinadora es una cinta de fibras largas, totalmente paralelizadas y limpias, esta cinta debe cumplir con peso y longitud determinados, el peso es de 70GN/ yarda. La cinta se deposita en botes de 24 pulgadas de diámetro por 43 pulgadas de altura, a los cuales le caven 7500m.
Sub producto.El subproducto de la peinadora es el noils el cual esta formado por las fibras cortas.Cinta de revientes y enredos.
Material Entrante.
El material entrante de la peinadora son los rollos de napa que produce la reunidota, estos rollos deben cumplir los siguientes requisitos.1. Los rollos de napa deben ser enteros no interrumpidos2. La masa de fibras o napa, debe estar libre de grasa, humedad, tramos gruesos, tramos delgados, repelados, basuras.3. Los tacos en los cuales esta envuelta la napa, deben estar en buen estado.4. Los rollos de napa deben cumplir con un peso y longitud determinados, estos rollos son de dos tamaños, para facilitar el cambio, y no tener la maquina parada por mucho tiempo. Los rollos enteros deben pesar aproximadamente 27.630g.
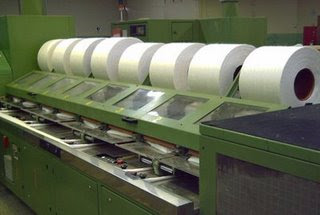
flujo de peinadora
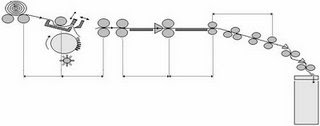
Tiene por objeto dar un adelgazamiento a la masa de fibras, hasta convertir la cinta de manuar en una mecha o pabilo, con una pequeña torsión para que resista la envoltura y manipulación en el proceso siguiente.En la mechera se cumplen las siguientes funciones:
La mecha o pabilo es depositado sobre una carreta plástica, formando un paquete deforma especial.La torsión es insertada en el pabilo estirado para darle resistencia. En una cinta haysuficiente masa de fibras para que estas permanezcan juntas sin necesidad de dar torsión.El retorcido del pabilo distribuye las fibras en un ligero ordenamiento en forma de espiral,para permitir que ellas se adhieran entre sí. La torsión que se da al pabilo debe de ser lasuficiente para que éste se envuelva fácilmente en la carreta y para que luego sedesenvuelva sin problemas cuando se alimente a la hiladora.El exceso de torsión disminuye la productividad de la mechera y causa trastornos durante elestiraje en la hiladora. Es por eso que la cantidad de torsión a insertar en una mecha debeser cuidadosamente evaluada.Formación del paquete• Formación de capas: El pabilo debe ser colocado sobre la carreta, cuidadosa yuniformemente durante la formación del paquete. La máquina coloca las espiras depabilo lado a lado, vertical y horizontalmente. La dirección vertical forma una seriede espiras y la horizontal una serie de capas.• Envoltura: El pabilo debe ser envuelto sobre la carreta a una rata de velocidad demanera que, no tenga ni mucha tensión ni quede muy flojo. Un paquete bienenvuelto es aquel que tiene la densidad deseada, es decir que no esté ni muy tenso nimuy flojo en su movimiento desde el cilindro frontal a través de la volante y sobrela carreta. Para obtener una buena envoltura, la máquina debe estar ajustada paradar una tensión correcta y constante a medida que cambia el diámetro del paquetecon cada capa de pabilo que se agrega.• Construcción de la envoltura: Como capas sucesivas de pabilo son envueltas sobrela carreta, el número de espiras por capa disminuye gradualmente en la partesuperior e inferior de la carreta con el fin de dar cierta conicidad al paquete. Laconstrucción cónica de la envoltura está estrictamente asociada con la operación deformación de capas. La mechera tiene un mecanismo de construcción de envolturaque hace posible darle al paquete una forma apropiada para que resista el manejo.Otro propósito de la construcción de la envoltura, es colocar la mayor cantidad depabilo sobre la carreta sin que ocasione problemas en la saca, transporte, atril yalimentación en las continuas de hilar.El paquete de pabilo tiene dimensiones determinadas de acuerdo al formato de la máquina.Las más comunes son 10 x 5”, 12 x 5 ½ “, 14 x 6 ½ “. Donde el primer número indica lalongitud y el segundo el diámetro del paquete.Una mechera normalmente tiene 96 ó 108 puestos de trabajo y cuando se produce untrastorno en alguno de ellos es necesario detener la marcha de toda la máquina.Cuando se produce un reviente de la mecha en algún puesto de trabajo ésta es succionadapor una corriente de aire que actúa mientras se detiene la máquina. Estas fibrassuccionadas son llevadas a una cámara especial donde se recolectan y luego se extraencomo subproducto, el cual es conocido como Pneumafil. Este se considera de alta calidad yes reprocesado nuevamente mezclándolo con algodón de pac
Funciones del Operario.Revisar contador:
Material Saliente.
El material saliente de la mechera es un pabilo con un titulo determinado ( Ne). Este pabilo se enrolla en una carreta plástica, la cual mide 395 mm de longitud y 61 mm de diámetro. La carreta tiene estrías en la base para la tracción y una pestaña para asegurar la punta del pabilo, las carretas tienen diferente divisa para diferenciar el titulo. A cada carreta le caben 2200 m de pabilo 1 Ne.
Subproducto
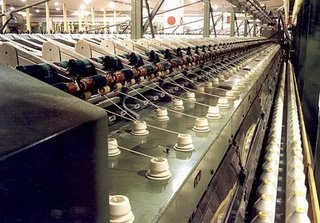
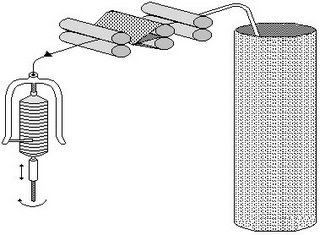
HiladoraEn éstas máquinas se obtienen los hilos propiamente dichos. Hay varios tipos de hiladoras,pero las universalmente conocidas son la hiladora de anillos y la hiladora por rotor
Consiste en dar el último estiraje al material, hasta obtener un hilo con un título determinado, aplicándole una torsión según el uso final y seguidamente devanarlo en una bobina.Los hilos más delgados son fabricados con doble pabilo, con el fin de buscar una mejor igualdad en el hilo.En esta máquina se cumplen las siguientes funciones:
Para el número inglés
AL igual que en la Mechera cuando se inicia la formación de las bobinas (husada o saca),se inicia para todos los husos a la vez y cuando se produce un reviente del hilo en algún puesto de trabajo éste es succionado por una corriente de aire que actúa mientras seempalma dicho hilo. Estas fibras succionadas son llevadas a una cámara especial donde serecolectan y luego se extraen como subproducto, el cual es conocido también comoPneumafil. Este se considera de alta calidad y es reprocesado nuevamente mezclándolo conalgodón de paca.Cuando una bobina sale defectuosa es rechazada y el hilo de subproducto es conocido comoestopa, la cual no se puede reprocesar para hacer nuevos hilos debido a la torsión insertada.
El material saliente de la hiladora es hilo de un titulo determinado (Ne) y una torsión definida.este hilo se envuelve en bobinas con diferentes divisas para separar los diferentes titulos. La bobina pesa 42g y mide 240 mm, el material pesa aproximadamente 106.5g ya que no todas las bobinas salen iguales, por que cuando hay un reviente la hiladora no para.
El subproducto que genera la hiladora es el pneumafil, que es el desperdicio del pabilo generado por revientes y enredos.
NORMAS DE SEGURIDAD
Equipos de Proteccion Personal.
el flujo de hiladora anillHiladora por Rotor o hiladora Open End
En esta máquina se cumplen las siguientes funcio
Cada puesto de trabajo es alimentado con una cinta proveniente de manuares (no con unpabilo).
La cinta alimentada recibe una limpieza extra
Se da un alto estiraje a la cinta reduciendo su masa al mínimo.
Se le da una alta torsión a la diminuta cinta formando el hilo propiamente dicho.
El hilo recién formado es devanado en forma de bobina cónica o cilíndrica (cono oqueso)
El hilo puede ser purgado: O sea, se eliminan los defect}
El hilo puede ser parafinado (lubricado): Sólo cuando se destina para tejido de punto.La máquina Open End puede tener hasta 240 puestos de trabajo repartidos a ambos lados dela máquina. Cada puesto trabaja independiente de los otros, o sea que mientras uno estaempezando a formar un cono otro puede estar finalizando.En este proceso también se obtienen dos subproductos uno en forma de pneumafil y el otrocomo estopa.La hilatura por rotor es una tecnología relativamente nueva, se usa desde 1967, tiene un altogrado de automatización y alta velocidad de producción. Comparando éste sistema con lahilatura de anillos, la hiladora por rotor hace el trabajo de la mechera, de la hiladora mismay de la enconadora. Fliujo Hiladora Open End
el flujo de hiladora open end
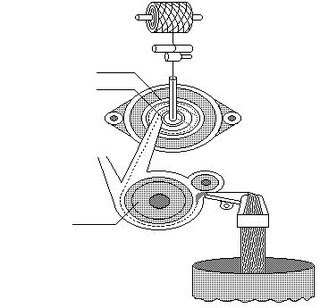
DIFERENCIAS ENTRE LOS HILADOS DE ANILLO Y LOS HILADOS OPENEND
Tienen mejores valores de irregularidad
Tienen mayor elongacionTienen menos partes gruesas y de
Guía hilos: Son ganchos encargados de guiar los hilos, también hay guía hilos de cerámica.Pesas de tensión: Son arandelas de diferente color y peso dependiendo de la tensión que se requiera.
3. Buena tensión.
5. Buen diámetro
6. No tener hilos abiertos.
Divisas.

el flujo de dobladora
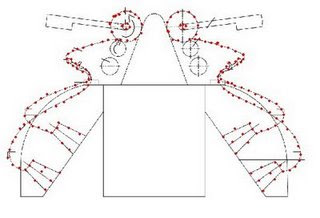
Devanar el hilo retorcido en una bobina, cono o queso, dependiendo del tipo demáquina.
Material Entrante.
Material Saliente
Subproducto.
NORMAS DE SEGURIDAD
el flujo retorcedora
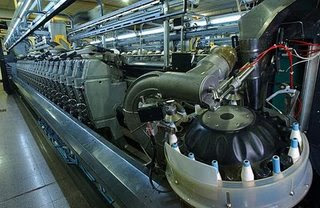
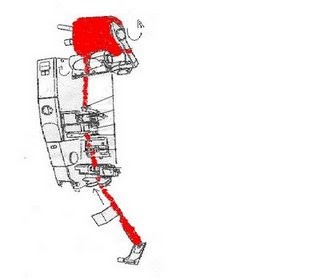
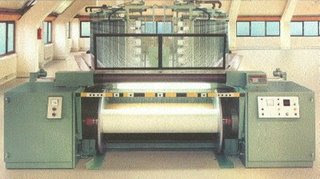
15. Engomado
En el engomado de hilos de urdimbre, no es menos importante que cualquiera de los procesos anteriores, por que de el depende la obtención de un buen tenor
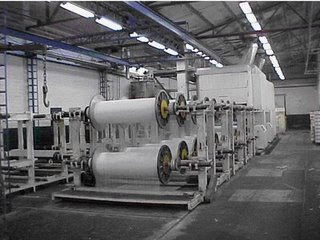
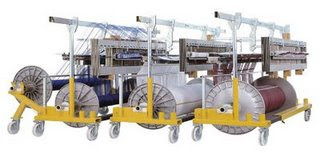
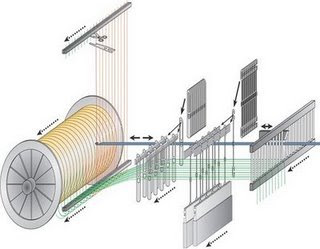
Telar convencional
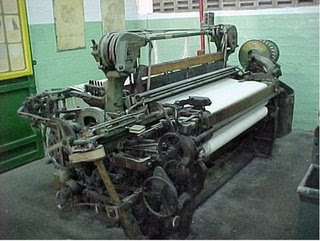
Son todos aquellos que hacen la inserción de trama por medio de un método diferente de la lanzadera y siempre en una sola dirección.
18. Tejido de punto

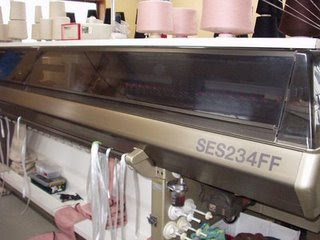
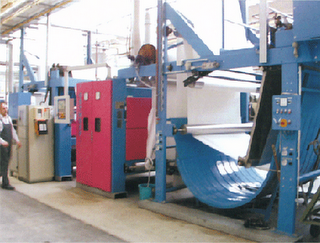
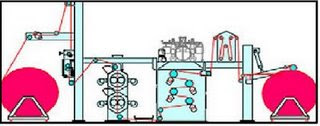
En esta operación, previa al teñido, se remueve el agente encolante empleado para los tejidos planos. El desengomado puede ser ácido o enzimático. Para ello pueden utilizarse enzimas ácidas, detergentes alcalinos y jabones disueltos en agua, para posteriormente enjuagar la tela.Los efluentes de desengomado enzimático del algodón presentan un aporte contaminante de 1000 a 6000 mg/l con una composición de solidos totales de 5000 a 20000 mg/l y un PH aproximadamente neutro. Por cada tonelada de producto se emplean de 5000 a 20000 litros de agua. (Agente encolante al 10%.)
Es la eliminación de los productos utilizados para el engomado de fibras.Los hilos provenientes de hilados se sostienen a la acción de gomas (almidón) y suavizadores (cebos) para darle consistencia y suavidad para el trabajo de telares.El desengomado se hace porque la tela que contiene las sustancias anteriores no es hidrófila, es decir, no absorbe agua y dado colorantes se disuelven en agua para aplicarlos después resultaría la tela mal teñido
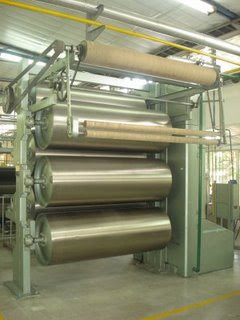
21. Descrude
Tiene por objeto la eliminación por saponificación o emulsion de las ceras o materias grasas del algodón, de las materias pectinicas, de los colores naturales del algodón, de cascaras y pelusas de la semilla.El descrude puede ser llevado a cabo bajo presión en ollas, o sin presión generalmente a la continua; ambos casos se utiliza una solución alcalina en presencia de un
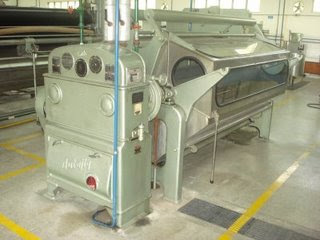
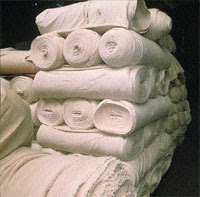
blanqueo
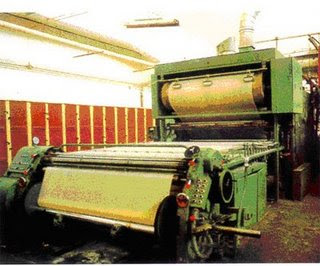
23.Sanforizado
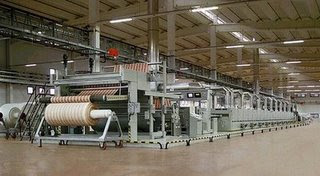
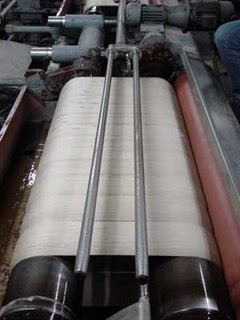
Es la etapa más compleja dentro de las operaciones de procesamiento; involucra una gran variedad de colorantes y agentes auxiliares de teñido. La calidad de la tintura depende del equipamiento empleado, la fórmula específica, los tintes y auxiliares de tintes que proveen el medio químico para su difusión y fijación sobre la fibra. La tintura puede realizarse en procesos discontinuos o de agotamiento y en procesos continuos o de impregnación. En esta etapa la dificultad encontrada es que los auxiliares usados en este proceso matizan los colores.Los procesos discontinuos de agotamiento se caracterizan porque el material textil está un tiempo más menos largo en contacto con el baño de teñido, dando tiempo a que el colorante se fije en la fibra. El proceso se realiza de diferentes maneras: a) Con el material en movimiento y el baño en reposo, para lo cual las máquinas más comunes son: La barca de torniquete: se usa básicamente para el teñido de tejidos de punto o jersey, felpas, alfombras y tejidos planos. La relación de baño, volumen de baño por kilo de material que se procesa, varía entre 1:30 a 1:15. Las relaciones de baño altas elevan el costo del teñido ya que para obtener la misma calidad de producto se requiere un mayor consumo de energía, colorante y productos auxiliares. El jigger: en esta máquina se trabaja solamente tejidos planos, como popelinas, driles, cretonas y felpas. Hay mayor velocidad de circulación de la materia textil en forma de cuerda. La relación del baño promedio es de 1:15, con el consiguiente ahorro de productos auxiliares, agua y energía. b) Con el material en reposo y el baño en movimiento Este proceso se utiliza para el teñido de hilados, ya sea en forma de madeja, conos, bobinas, tejidos de punto sintético y tejido plano. Se utilizan autoclaves verticales u horizontales. c) Con el material y el baño en movimiento Con este método se ha conseguido el aumento de la producción de teñido, mejorando notablemente la uniformidad y el aspecto final de las telas. Las máquinas jet y overflow trabajan a altas temperaturas donde el movimiento del material no depende de un torniquete, sino de la inyección del baño por medio de una bomba que lo toma de la parte inferior de la máquina, para hacerlo pasar por una tobera Venturi, lo que permite teñir a velocidades de circulación muy elevadas. La relación del baño promedio es de 1:10 y se emplea tanto para tejidos planos como de punto. Lo+B18s procesos continuos o de impregnación se usan principalmente para la tintura de tejido plano, aunque, para determinados colores, también se aplica a tejidos tubulares (de punto). La tela pasa en forma continua por un foulard que contiene una solución concentrada de colorantes y auxiliares. Luego se exprime y se fija el colorante ya sea por reposo en una cámara, o por medio de vapor en una vaporizadora o por calor seco a alta temperatura en una instalación thermosol. Los tipos de fijación varían de acuerdo al colorante utilizado. El tipo de colorante empleado en la tintura determina los auxiliares utilizados: sales de sodio, cloruros, sulfatos y carbonatos como agentes sinergistas. Si bien en la actualidad se tiene la tendencia de suprimirlos, en tratamientos posteriores se emplean sales de cobre y cromo para la fijación de algunos colorantes, lo que mejora la solidez. Los colorantes directos sustantivos son sustancias neutras que tienen gran afinidad con el algodón y la celulosa en general. Debido a su alta solubilidad es necesario utilizar sales (cloruros o sulfatos) para obtener un agotamiento óptimo. El efluente procedente de estas tinturas no es muy contaminante, pero presenta un alto grado de coloración. Los colorantes tina son insolubles en agua, por ello se utilizan agentes reductores fuertes, tales como el hidrosulfito en medio alcalino que los transforman en la correspondiente forma leuco y en esa forma sube sobre la tela. Luego se efectúa la oxidación sobre la tela, al aire, con perboratos o con H2O2. Posteriormente se debe eliminar el exceso de álcali con lavados en caliente. Cada uno de estos pasos está seguido de un enjuague en caliente. Generalmente estos colorantes provocan efluentes con altos valores de contaminantes. Los colorantes al sulfuro, como su nombre lo indica, contienen compuestos sulfurados en su estructura y se aplican en la fibra en estado reducido disueltos en sulfuro de sodio para luego oxidarse produciendo la coloración esperada. Las aguas de desecho contienen el baño de tintura y los enjuagues son alcalinos, altamente coloreados y tóxicos y constituyen uno de los efluentes más contaminados. Ha surgido una línea de colorantes llamados "sulfuros ecológicos" que utilizan otro tipo de reductores y requieren una menor cantidad de sulfuro de sodio para su disolución. Existe una tendencia mundial a no usar los colorantes al sulfuro. Colorantes en base naftol: azoicos insolubles. El tejido se impregna primeramente con un agente de desarrollo como el naftol; se exprime y eventualmente se seca en forma suave y luego se trata con una base diazotada o su correspondiente sal soluble para que se produzca el desarrollo (o copulación) del color, generándose en la fibra. Luego de la copulación se enjuaga jabonando enérgicamente y a ebullición. Los contaminantes principales se originan en las tinturas diazota- das, el beta-naftol y los enjugues. Colorantes reactivos: son los únicos colorantes que se unen a la fibra químicamente. Para ello inicialmente se disuelve el colorante y luego se agota con grandes cantidades de sal para lograr el desplazamiento del colorante hacia la fibra en el menor tiempo posible, evitando la hidrólisis del mismo en el agua que compite con la subida del colorante a la fibra. Inmediatamente se fija en medio alcalino (carbonato, hidróxido o silicato de sodio) entre 50 y 80 oC. Los enjuagues comprenden lavados jabonosos a ebullición y un aclarado final con agua
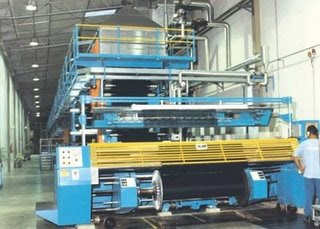
26. Estampacion:
Es un teñido local. Es la técnica de decorar un tejido, con determinado dibujo, utilizando solamente un espacio especifico en la tela. Emplea los mismos colorantes que se utilizan cuando se tiñe completamente, pero con la ventaja de que aquí se pueden emplear varios colores separados, para dar un efecto multi color al genero. Puede pensarse como una técnica de pintar un dibujo en una tela
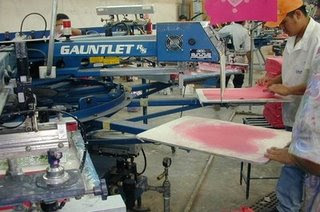
27. Revisiojn final.
Cada metro de tela es inspeccionado visualmente usando el sistema de evaluacion de 4 puntos. La informacion es introducida atravez de un sistema de refuerzo para lograr una optimizacion en el corte. Enseguida la tela pasa por mesar de corte en donde la pieza es cortada en rollos de tela, deacuerdo tambien a las especificaciones de el cliente
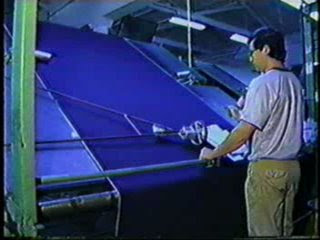
No hay comentarios:
Publicar un comentario